Table of Contents
Ever since the game of cricket became a professional sport, there have been many changes to it. However, the one thing that has remained constant is the shape and feel of the bat. There have been changes to its size and method of preparation but which has made it into the giant version that the cricketers use today. Several altercations such as the increase in width of the bat, multiple grips, oiling, and hammering are practiced in modern-day cricket.
Let’s talk about how the cricket bats are made.
What Tools Do You Need to Make a Cricket Bat?
One would need multiple tools to make a cricket bat. Below listed are some of the tools we need in making a cricket bat:
- Draw Knife/Pod Shaver – Pod Shaver is a traditional title. It is a staple tool of the bat maker. Brades is a type of drawknife from the 1930s. Pre-World War 2 British Steel is always considered good quality.
- Shaping Plane – Shaping Plane is another old tool for a relatively new bat shape. It’s a wooden box plane, with a rounded base and blade. It is used to make concave-shaped backs which are very popular in modern bats.
- Smoothing Plane – The smoothing plane is used for shaping the edges of the bat.
- Glue Knife – Glue knife is used to open breaks for gluing while repairing old and damaged bats. To make it more comfortable, the handle is taped up.
- Sanding Gloves – Hand sanding comes in the final stages of bat finishing. Start with a very coarse 80 grit and work till a fine 320 grits. The sand can be very hard and rough on the hands therefore gloves are necessary. A wicket-keeper’s glove liner can also be used.
- Rubber Grip – A rubber grip is the last task in bat finishing. Once the bat is ready, you should apply a rubber grip on the handle of the bat.
What Material is Used to Make a Cricket Bat?
A cricket bat can be made from 3 different willows which are listed below:
- Kashmir Willow – Kashmir Willow, as the name suggests is found in the regions of Kashmir. Even though the Kashmir quality willow is excellent, it is not as popular as the English willow. Therefore, it is the main raw material for companies that do not operate on a large scale and make cheap bats.
- English Willow – English willow bats are made of clefts that are imported from the United Kingdom. These willows are considered better than the Kashmir Willow and are used by most international players. Prominent bat makers and brands also use English willow who make expensive bats.
- White Willow / Salix Alba – White willow or Salix Alba is a native to Europe and western and central Asia. The wood is tough, lightweight, and shock-resistant. This means it can handle the high-speed impact of the cricket bat without harming the bat.
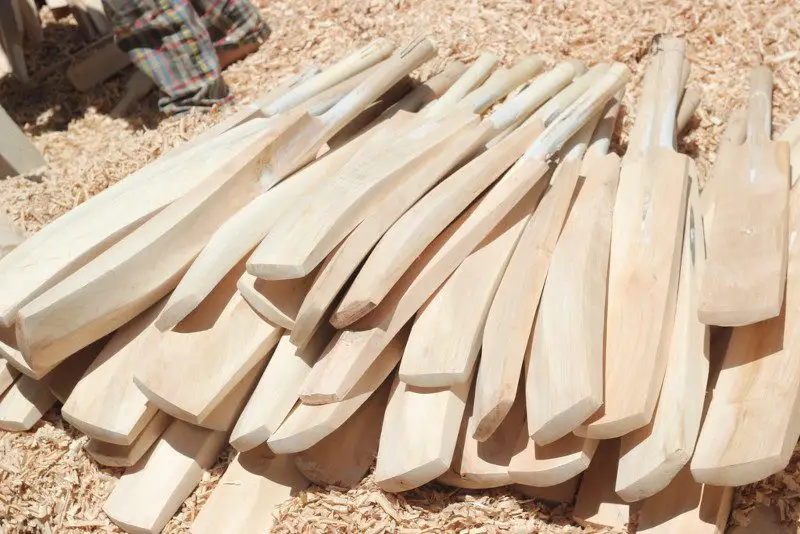
How Can I Make a Cricket Bat at Home?
A genuine cricket bat can be difficult to make at home. It carries a set of difficulties with itself which is not a feasible option for a bat creation. One cannot manually make a cricket bat, we need automated machines for the main operations. A craftsman can still perform functions such as the shaping of the bat. The above-mentioned tools are a handy guide for a person to start the bat-making process. Apart from proper tools and machines you also need a proper location, a place with good lighting and electricity supply. One cannot afford to make any mistake especially while shaping the bat.
How is a Cricket Bat Made Step by Step?
Making a cricket a cricket bat is a well defined process. The main phases of manufacturing a cricket bat are listed below:
1. Cutting or Machining Process
The process starts with cutting or machining the willow. The trunk of the willow is given an approximate shape which is known as clefts. Before a perfect shape is given, their ends are dipped in wax. This wax is air-dried for approximately a year’s time. Clefts are then graded into four levels on the basis of straightness, width, blemishes, etc. The size of the bat should not be more than 38 inches and the width should not exceed 4.25 inches.
2. Pressing Process
As the name suggests, the pressing process involves pressing the fibres close. This helps in shaping the bat through compressing and making it a solid compact willow. It is one of the most important steps of bat making that will eventually define the performance and durability of the bat.
3. Fitting the Handle
After the pressing process, the blade is sliced at the top to create space for a handle to be attached. The handle is fixed into this space and the adhesives are applied. The handle is key in providing the bat with spring like capabilities and forms an essential part of the bat.
4. Shaping the Bat
A draw knife is used in giving a desired shape to the bat. The altercations are more specific in nature such as rounding off the toe and filing away the unnecessary pieces.
5. Finishing Operations
Once the edges and the face has been sanded down, which makes the bat smoother, the bat is then polished by a bee wax compound. This helps in keeping the moisture out and letting the linseed oil in. Once the handle is bound, a string of rubber is then applied on the handle which gives the batsman a desired grip on the bat and also gives it a smoother feel, making it easier to hold. A toe guard along with the brand sticker is then applied.
Conclusion
Thus, we can conclude by saying that making a cricket bat is always an option. But as mentioned above you need to have the necessary material, tools and location to give justice to the same. Else there are multiple bat manufacturers around the world from whom you can purchase your desired bat. Just like any other product, even a cricket bat is available in cheap and expensive options.